Why are Centralized Lubrication Systems are important in Industrial Settings?
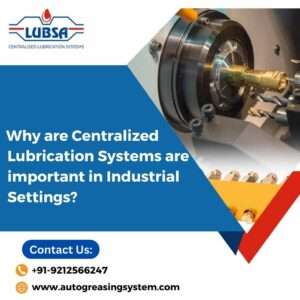
An effective lubrication system plays an essential part in the industrial setting, where machinery runs nonstop. It is essential to choose the correct Centralised Lubrication Systems Supplier in order to guarantee maximum machinery performance, extended lifespan, and less downtime. This is to examines the benefits of a Centralised Lubrication System in industrial applications as well as the critical elements of selecting a trustworthy supplier.
Using Centralised lubrication systems, different industrial components receive precisely the right amount of lubricant, streamlining the lubrication process. This improves overall operating efficiency by lowering wear and friction as well as the need for maintenance.
Industrial machinery must work in harsh environments. By ensuring that every component continually receives the required lubrication, Centralised lubrication systems help to reduce premature wear, overheating, and potential malfunctions.
Selecting the Ideal Centralised Lubrication System Manufacturer
Experience:
- Give preference to Centralised lubrication system designers and producers who have a track record of success.
- Take into account their experience in a range of industrial applications, demonstrating a thorough comprehension of various machinery needs.
Customization Abilities:
- Assess the manufacturer’s capacity to modify lubricating systems to meet the requirements of particular machines.
- Optimal performance in various industrial setups is ensured by a provider offering customized and adaptable solutions.
Component quality:
- Check the quality of the parts and materials that go into making lubricating systems.
- Superior components reduce the likelihood of malfunctions by enhancing the system’s dependability and robustness.
Compliance to Industry Standards:
- Verify the Centralised Lubrication System Manufacturer to pertinent industry certifications and requirements.
- Ensuring compliance guarantees that the lubricating systems fulfill the essential safety and performance standards, signifying a dedication.
Post-purchase Assistance:
- Take into account the availability of thorough after-sales support, which includes easily available spare parts and maintenance services.
- In order to maximize uptime and ensure the lifespan of the lubrication system, responsive support is essential.
Cost-effectiveness:
- Prioritize the entire value that the lubricating system offers, even while cost is a concern.
- Even while a dependable system would cost more up front, over time it can save a lot of money because to lower maintenance requirements and better machinery performance.
Citations and Evaluations:
- Ask for recommendations and endorsements from other companies that have used the lubricating systems made by the manufacturer.
- Feedback from customers in the real world sheds light on the effectiveness, dependability, and general contentment with the supplier’s goods.
Technological Innovation and Progress:
- Evaluate the manufacturer’s dedication to innovation and keeping up with industry technical changes.
- Providers who invest in modern technologies may offer solutions that align with evolving industrial needs and advancements in lubrication system design.
How to Evaluat the Lubrication System Suppliers?
- Give preference to vendors who have a strong track record and a wealth of knowledge when it comes to developing and implementing lubricating systems.
- Examine the Lubrication Systems Supplier capacity to adapt solutions in accordance with particular machinery specifications, guaranteeing a customized approach to lubricating requirements.
- Verify the longevity and dependability of their lubricating systems by inspecting the materials and parts utilized.
- Verify the supplier’s adherence to industry certifications and standards to make sure their products fulfill performance and safety requirements.
- In order to ensure continuous functioning, assess the responsiveness and availability of after-sales support, including maintenance services and spare parts.
- Evaluate the total value provided by the lubrication systems provided by the provider, balancing the initial investment against long-term maintenance savings and enhanced machinery performance.
- For actual feedback on performance and satisfaction, look for references and testimonies from other companies that are utilizing the lubricating systems provided by the provider.
- For long-term relevance, evaluate the supplier’s innovation commitment by keeping abreast of technical developments in lubricating system design.
- Global suppliers may provide more resources, knowledge, and assistance, guaranteeing dependability and scalability in a range of industrial contexts.
Benefits of a Centralised Lubrication System
- Proper lubrication prolongs the life of equipment components by reducing wear and friction.
- Lubrication that is automatic and continuous reduces the need for manual intervention, which lowers downtime for repairs and maintenance.
- Centralised lubrication systems maximize the performance and efficiency of machinery by ensuring that each part receives the proper quantity of lubricant.
- Effective lubrication lowers energy and maintenance expenses, which has long-term financial advantages.
- The technology ensures maximum performance without over-lubricating by precisely delivering lubricant quantities to each component.
- Maintaining proper lubrication lowers the possibility of equipment failures and malfunctions, improving worker and operator safety at work.
- A major benefit of Centralised systems to the sustainability of the environment is the reduction of lubricant waste and runoff.
- Centralised lubrication systems are adaptable and may be tailored for a wide range of industrial uses, including heavy machinery, automobile assembly lines, and manufacturing facilities.
- Centralised solutions frequently streamline maintenance procedures, facilitating operator management of lubrication schedules and lowering the risk of error.
Application Areas for Centralised Lubrication Systems
Numerous industrial industries find significant uses for Centralised lubrication systems. These technologies maximize the efficiency of complex machinery in manufacturing facilities, guaranteeing smooth production lines.
Automated and constant lubrication improves the longevity and operating efficiency of heavy machinery used in mining and construction. Centralised lubrication is essential to the dependability of the precision assembly lines and robotic systems used in the automotive industry.
Strong and dependable lubricating systems are required to ensure maximum performance in the harsh circumstances of steel mills, which are typified by high temperatures and heavy-duty activities. Centralised lubrication systems are extremely useful in many different sectors because of their adaptability, which improves the lifetime and performance of machinery.
The right Centralised Lubrication Systems Supplier is essential to success in the complex web of industrial processes. The benefits of a well-designed and executed Centralised Lubrication System are numerous, ranging from increasing machinery lifespan to decreasing downtime and improving efficiency.
Businesses looking to optimize the advantages of Centralised lubrication in their operations must carefully evaluate the supplier’s experience, ability to customize products, and dedication to quality. Accept the longevity and efficiency that a dependable lubrication system offers, opening the door to smooth industrial operations and long-term prosperity.